Възстановяване на авточасти
Възстановяване на авточасти
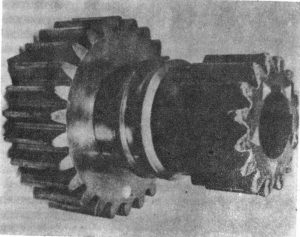
През втората половина на 80-те години, наред с усьвършенстването на автомобила, постигането на по-високи скорости, олекотяването и опростяването на конструкциите, подобряването на комфорта и надеждността, сред някои производители особено актуални стават и проблемите я възстановяване работоспособността на отделните части, възли и агрегати. Предвижда се, че в близко бъдеще учените и техниците все по-често ще се срещат с дилемата: да се бракува ли даден детайл, или да се възстанови с подходящи методи.
Възстановяването на авточасти като метод не възниква спонтанно, а е плод на дългогодишни усилия. То е пряко свързано с развитието на много науки — химията, физиката, технологията и рязането на металите, електрохимията – и ще се развива заедно с тях.
Изгодно ли е възстановяването? Конструктивните особености на съвременните автомобили, изискванията я точност на детайлите и хлабината между тях са такива, че отделните агрегати и възли се бракуват при увеличаване на хлабината между взаимно работещата двойка детайли до 0,2—0,6 милиметра. Практиката показва, че 90 процента от детайлите, отнесени към негодните, имат износване 0,1—0,3 милиметра по диаметър. За голяма част от тях това означава загуби, по-малки от един процент от масата им.
Икономическата целесъобразност от възстановяването на частите се определя от възможността повторно да се използват 65—75 процента от тях, което означава да се икономисат парични средства, метали и материали, да се намали разходът на нови резервни части, да се освободят производствени мощности в машиностроенето. Себестойността на възстановените части не превишава 75 процента от стойността на новите, а разходът на материали в тяхното възстановяване е 15—20 пъти по-нисък.
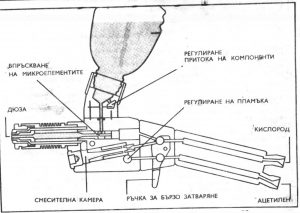
Износването на детайлите не може да служи като причина за бракуване, а е само основа я възстановяване. В зависимост от големините на износването, вида на частите и условията, при които работят, се използват най-разнообразни методи за възстановяване
Всеизвестни са различни по-стари методи я възстановяване: механична обработка до ремонтен размер, поставяне на допълнителни части , обработка под налягане и т. н. През втората половина на 80-те години все повече се разпространяват такива ефективни методи като напластяване (наваряване), метализация, нанасяне на галванични или пластмасови покрития.
Напластяване. При този метод върху повърхността на дефектния детайл се напластява (наварява) стопен метал, след което детайлът се обработва механически. Особено висока производителност и качество осигуряват механизираните методи за напластяване.
Източник на наварен метал е електроден тел, който се стопява от електрическата дъга, образувана между него и повърхността на детайла. В зоната на горенето се подава сух зърнест флюс, който покрива дебел стой от наварявания участък. Отделящата се при горенето на дъгата топлина стопява електродния тел, повърхностния слой метал на детайла и част от флюса. Стопеният флюс образува еластична покривка, която защищава заварката от атмосферните влияния. Флюсът служи не само за защита на напластения метал, но и за легирането му. Освен това, благодарение на него се намаляват и изгарянията и се запазва топлината.
С напластяване под слой флюс се възстановяват такива детайли като шийките на коляновия вал, карданни валове, шлицевият край на полуваловете, гърбиците на разпределителния вал.
При вибродъговото напластяване се използва електрод, който вибрира с помощта на електромагнитен вибратор, като електродният тел се топи под действието на импулсни електрически разряди, постъпващи от източника на ток. Този метод се отличава с високата си производителност.
На долната снимка виждаме устройство за електродъгово напластяване: 1— Основен метал; 2— Предпазен пласт; 3— Флюс, който предпазва стопилката по време на охлаждането; 4— Газово покритие; 5 — Електрод; 4 — Микроелементи, които се съдържат в електрода; 7 — Електрическа дъга с голяма мощност
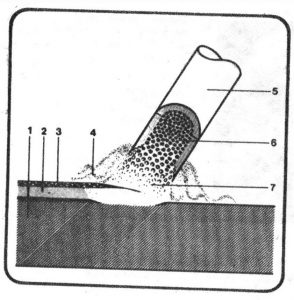
Особен интерес представлява плазмено-дъговото напластяване. Плазмата е йонизиран газ, представляващ електрически неутрална смес от положителни, отрицателни и неутрални частици. Тя се характеризира с висока електропроводимост и голяма топлопроводност, вследствие на което образува около себе си магнитно поле. Като плазмообразуващ газ най- често се използва аргон или хелий. В плазменото поле от електрода се отделя стопен метал, който се нанася върху детайла. За този процес се използува устройство, наречено плаз- мотрон.
Съоръженията за напластяване – наваръчен автомат, газоелектрическа горелка, плазмотрон – могат да се монтират дори на обикновен винтонарезен струг.
Друг интересен процес е метализацията. При нея върху предварително подготвената повърхност на детайла се образува покритие чрез нанасяне на частици разтопен метал с помощта на въздух под налягане или инертен газ. Източникът на метал се използва във вид на прашец или на тел. Дебелината на нанесения метален слой може да бъде от 0,03 мм до няколко милиметра. На метализиране могат да се подлагат не само метали, но и пластмаси, дърво, стъкло, гипс. Затова метализацията може да се използува за възстановяване, а също и като метод за нанасяне на антикорозионни и декоративни покрития. Газовата метализация намира приложение и за превантивно метализиране на детайли при производството на нови автомобили. Например компанията FIAT използва метализацията на детайли, за да се подобри тяхната износоустойчивост. Употребяват се молибденов тел и два вида тел от сплави на цветни метали. В бившия Съветски съюз и по-точно във Волжския автомоблостроителен завод някои детайли са метализирани с металокерамична тел, която също съдържа молибден.
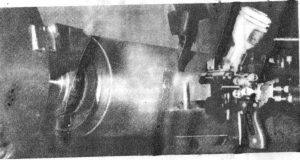
Устройството за напластяване, в което се използва процес „Рототек 80“
Може би звучи парадоксално, но благодарение на метализацията могат дори да се произвеждат детайли от по-евтини въглеродни стомани, чиято повърхност се метализира и придобива значително по-високи качества от тези на основния метал.
Възстановяването на части с галванични покрития се заключава в електролитно отлагане на метал върху предварително подготвената повърхност на детайла. В авторемонтното производство галванични покрития се използват за ремонт на износени повърхнини, за износоустойчиви и защитно-декоративни покрития. Най-разпространени са хромирането и ожелезняването, по-рядко се използват помедяването и никелирането. Познати са и други видове електрохимични обработки. Детайлите се поставят в специални електролитни вани и играят ролята на катод. По този начин се възстановяват авточасти с всякаква конфигурация — тласкач на клапана, бутален болт, мотовилки и други.
Пластмасовите покрития също добиха широко разпространение. Те имат редица ценни свойства, проста технология на нанасяне и са сравнително евтини. В някои случаи те са единственото средство за възстановяване на детайлите.
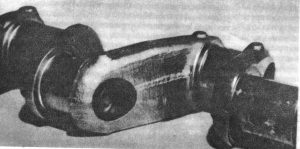
Най-голямо приложение в тези процеси намират капроновата смола, полиетиленът, стъклопластмасите, епоксидните композиции и синтетичните лепила.
Капроновата смола се използва за детайли с голяма износоустойчивост и високи антифрикционни свойства (черупки за различни лагери, зъбни колела и др.). С епоксидни смоли се възстановяват корпусни детайли с пукнатини и пробиви, а полиетиленът най-често се използва за уплътнения и изолации.
В последните години все по-широко се прилагат така наречените уплътняващи маси. Те са създадени на базата на синтетични лепила и намират приложение при възстановяването на износени лагерни легла, пукнатини и пробойни. Типично в това отношение е лепилото „Локтайт“. Пластмасите все повече заменят самите метали, което широко можем да наблюдаваме в съвременните автомобили.
Поглед в бъдещето. Огромната практическа стойност на възстановяването на детайлите като процес е очевидна. Суровинните проблеми на човечеството безспорно ще тласнат напред тази колкото привлекателна, толкова противоречива и многостранна наука. Защото тя се разпростира не само върху автомобилите, а и върху всички видове машини. Благодарение на нея се спестяват хиляди тонове метал, изтръгнат от недрата на нашата задъхана планета.
Вашият коментар